ARTICLES
From Clay to Art | What Ceramics Mean to Miyako Terakura
2022.10.20
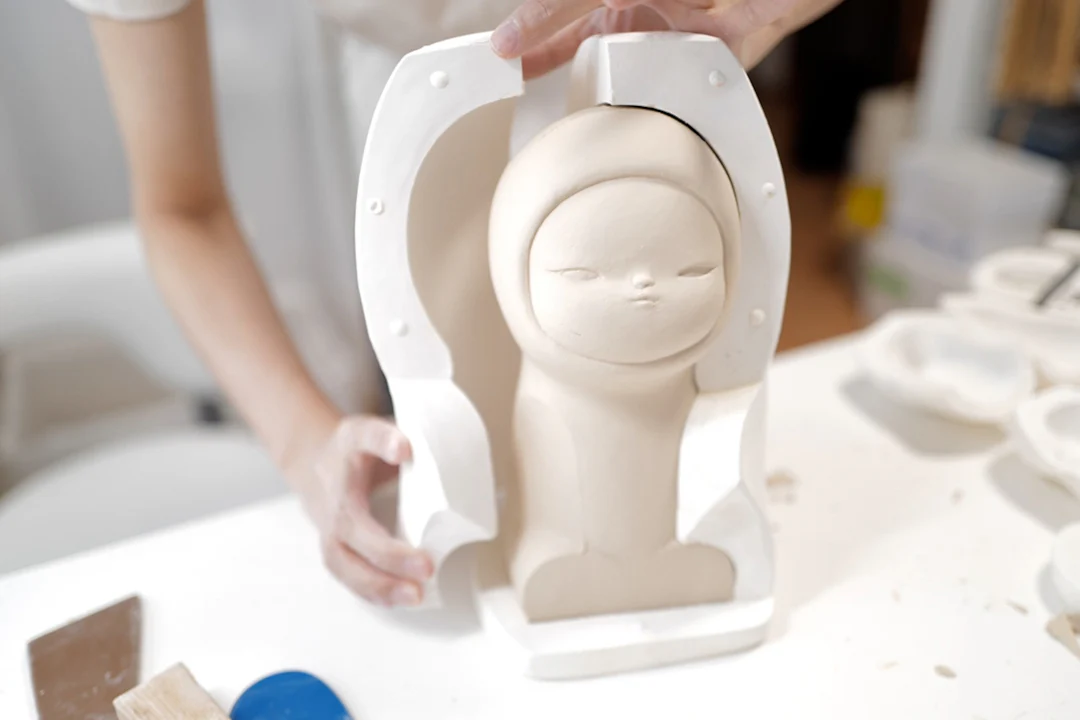
The "Fairy Whisper" duo exhibition that featured ceramic and wooden sculptures ended in great success at the Whitestone Gallery Taipei. The two artists both specialize in sculptures that depict infants and children. One of them is Miyako Terakura, who studied ceramics in the Tokyo University of the Arts, and has since pursued a career as a ceramic artist. We asked Terakura about her techniques for creating ceramic sculptures, and what she thinks is the charm of ceramic art.
Shaping Ceramics: Handbuilding and Slip Casting
There are many different techniques for shaping ceramics, but here we focus on two techniques known as "handbuilding" and "slip casting". Until recently, Terakura had mainly used slip casting, but for the Fairy Whisper exhibition held last September, she tried using handbuilding techniques for the first time.
Handbuilding
Handbuilding is a shaping technique that has been used since prehistoric times. It was used to make the Jomon pottery and Haniwa figurines in ancient Japan. The main characteristic of handbuilding is the complete freedom to shape the clay as one desires.
Terakura first places a rounded lump of clay on the center of a hand-spun potter's wheel to form the base shape of the sculpture. She then rolls a cylindrical piece of clay and places it on top of the base, carefully attaching the two pieces together while shaping it with her hands to prevent cracks from forming.
According to Terakura, "handbuilding involves pressing the clay not just from the outside but also from the inside. It's suitable for expressing a tight but soft, voluminous quality in a sculpture. When I form the face, I press the inside to puff the cheeks and press the outside to make small depressions, creating the soft curves and delicate facial expression."
Creating a sculpture from the "Fire" series using handbuilding
Slip Casting
The rabbit prototype and plaster molds for the "Moon and Rabbit" series
Slip casting is a forming technique that involves pouring clay slurry into a plaster mold. Meissen porcelain dolls are made using this method.
The general procedure for slip casting starts from: 1) making a prototype, 2) creating a casting mold using plaster, 3) making the clay slurry, then 4) pouring the slurry into the mold. Since there are many steps involved, the technique takes much time and effort. On the other hand, since the molds can be used repeatedly, it is ideal for creating multiple copies of the same sculpture. Furthermore, since porcelain clay is not suited for handbuilding, slip casting is usually the technique of choice for creating porcelain sculptures.
For slip casting, Terakura first makes a prototype using clay, then creates a plaster mold around the prototype. The more complex the sculpture's form is, the more molds are required.
The next step is casting, which involves pouring the slurry into the dried plaster molds to the brim. The plaster molds absorb water from the slurry, forming a cast layer on their inner surface. Since the molds need to be kept full at all times, she adds more slurry while waiting for the cast layer to attain the desired thickness. When the cast reaches the right thickness, she pours out the excess slurry from the molds.
Pouring the slurry into the dried plaster molds to the brim
After the ceramic layer inside the mold hardens to some extent, Terakura carefully removes the cast from the mold. While the ceramic is still soft, she adjusts the shape or smoothens the surface of the sculpture.
Removing the cast parts from the plaster mold
After removing all the parts from the molds, Terakura brushes off the connecting surfaces to make sure they fit perfectly, then uses slurry to attach the different parts together and complete the sculpture's form.
Attaching the different parts together in a rabbit sculpture from the "Moon and Rabbit" series
Regarding her approach to slip casting, Terakura says "I don't make the exact same copy every time. Each sculpture has its individuality and "soul" where I adjust their facial expressions after removing them from the molds. The differences might not be easily noticeable, but I always add a unique touch to each one.”
Choosing the Right Shaping Technique
When asked about how she chooses which shaping technique to use for her sculptures, Terakura says she decides on the appropriate technique based on the type and form of the artwork she wants to make.
"With slip casting, I can make the same form many times, so I often use this technique when I want to combine multiple sculptures into a single installation. Since porcelain is a white, fine-grained clay, it is not suitable for handbuilding, so I also use slip casting when I want to make a sculpture with a beautiful, white surface. With handbuilding, I have more freedom with the size and shape of the sculpture, so I use it when I want to meticulously create an item that is one-of-a-kind."
Defective casts and excess clay shavings are dried and reused as slurry
After Shaping Comes the Firing
From the first firing step, both hand-built and slip-cast sculptures follow the same process. Let's take a step-by-step look at how the ceramic sculptures are fired and finished according to Terakura's method.
Bisque Firing
For bisque firing, Terakura fires the sculptures for 8 to 12 hours at 800 to 900℃.
After letting the ceramic sculptures dry completely, they are fired for the first time in a process called "bisque firing". Depending on the size of the sculptures, they are fired between 8 to 12 hours at a temperature of around 800 to 900℃. After the bisque firing, Terakura polishes the sculptures with sandpaper to finalize their shape.
Underglaze Painting
After the sanding, Terakura applies colors to the bisque-fired sculptures using underglaze paint. Since underglaze paint changes color when fired, she also prepares test pieces that serve as color samples.
Color samples for underglaze painting
While using the test pieces as a reference and visualizing how the colors will appear after firing, Terakura applies each color in several layers. Besides paintbrushes, she also sometimes uses an airbrush to apply a color gradient effect.
A sculpture from the "Fire" series painted using an airbrush
Terakura describes her feelings for her sculptures' eyes as follows: "During the underglaze painting, I particularly put effort and emotion in painting the eyes. It feels like I'm giving the sculpture its soul."
Applying underglaze paint to the sculpture's eyes
Glazing
Sculptures from the "Moon and Rabbit" series with clear glaze on their eyes and matte glaze on their faces
After the underglaze painting, Terakura applies a glaze on top of it. Glaze turns into a glass-like substance when fired at high temperatures. By combining different materials together, she can express a variety of colors and textures on the sculptures. Different kinds of glaze can also be applied on a single sculpture.
Glost Firing
For glost firing, Terakura fires the sculptures for 15 to 17 hours at about 1,230℃.
The second firing at higher temperature is known as "glost firing". This firing causes the clay to shrink by around 10 to 20% of its original size. It also turns the glaze into a glass-like substance.
For Terakura, the appeal of ceramic art is in its transformation and uncertainty. "Inside the hot kiln, what was originally clay irreversibly changes to an entirely different ceramic material. By entrusting my artworks to another "power", an uncertainty arises in the resulting product, and I find this to be both the charm and agony of creating ceramic art."
Overglaze Painting
Overglaze paints
After the glost firing, the sculptures are further painted with overglaze and gold luster. For her sculptures, Terakura paints overglaze to add shine to the eyes, and to give a rosy tint to the cheeks, nose, and mouth.
A sculpture from the "Fire" series with shiny eyes from overglaze
Completion of the Sculptures
After painting the overglaze, the sculptures are fired for a third time at around 800 to 840℃. This third firing completes the ceramic artworks.
Miyako Terakura "The Kid of the Stars" (2022), 11.5×13.5×30.0cm, slip-cast porcelain/gold luster
"Fairy Whisper" exhibition installation view. Foreground: "The Little Fire Leading My Heart" (2022), hand-built clay. Background: "Fire" series (2022), hand-built clay.
For Terakura, the stress and excitement of making ceramic art builds up whenever she opens the kiln. "After the high firing, it takes about three days for the kiln to cool down before I can take the sculptures out. Opening the kiln is always an exciting moment, with a mix of expectation and anxiety."
Regarding her plans for the future, Terakura says "I want to continue being honest with my feelings and create whatever it is that I feel like making at that moment in time."
You can watch Miyako Terakura in the process of creating her sculptures in the "Fairy Whisper" online exhibition. Come and see the sculptures that transformed from clay to ceramic art through the magic of Terakura's hands.